Jet Mill

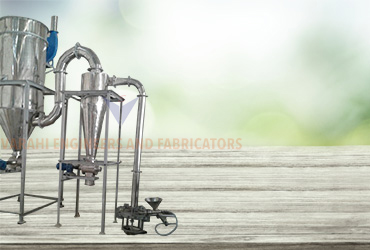
Use of jet Mill
Varahi Engineers and Fabricators Micronizer Jet Mill is to micronise Pharmaceuticals, Chemicals, Pigments, Minerals, Agrochemicals, Minerals and thermoplastics. It is also for heat sensitive, corrosive and abrasive Materials.
About Jet Mill
Micronizing as well as classification is to be done in varahi Jetmill by taking advantage of fluid energy. Micro Fine Jet Mill is designed to inject high pressure air or Steam in to cylindrical chamber through Specially designed Nozzles are placed at equally spaced on peripheral wall to have each Jet is tangential at imaginary smaller circumference. Ventury system is control fed role of material very precisely to get productivity. Jets are generate high velocity vorlex during material feeding which create vacuum to suck product into high speed vortex. Suspended particle of the material are collide with each other and reduce themselves by attrition as well as collision whenever it comes in strong velocity gradients near the jet. Micronized particles to get out with jet fluid through center of chamber and get collected into the cyclone collector system. Heavier or oversize particles are stay in to chamber until micronized due Centrifugal force.
Operating pressure in between 7-8kg/cm2, Average feed size of materials is 200 mesh, Adequate quantity of air. Controlled feed and microfine setting play an important role. All the data given are nominal only. It may vary widely from case to case depending upon many factors.
Benefits of our Design
Unique design to micronise wide range of dry solids material very economically and efficiently. Particle collide with each other without any moving part, which results absolute productivity and negligible maintenance. Provided interchangeable liners. Easy dismantle for cleaning and quick reassemble Is possible for cleaning and material change. Compact design require less floor space.
Benefits of our Jetmill
For example, 2 micron size particle improve product quality to great extent as compared to 325 -mesh particle in terms of efficiency, dispersion, behavior and intimate blends of different material. It is due to increase in number of particles and surface area It is also increase suspensibility. dispersion rate, surface area of particle and bulk density. Models selection different project and order
Design General or Pharma
Construction: MS, SS.
Wear reduction Liners OR lined chamber with different material. Different design Grinding chamber and venturi feeding system. Discharge: Top or Bottom.
Material collection : Cyclone, dust collector, pulse jet dust collector or their combination
Technical Data of Jet Mill
Model | Capacity Approx | Air Comp. HP | Air CFM FAD | Appx Space for Mill at Bagging HT=1000mm |
---|---|---|---|---|
kg/hr. | Pressure 7kg/cm2 | LXWXH Mtrs. | ||
VMF-4 | 3 | 20 | 45 | 1.0x1.0x1.5 |
VMF-6 | 10 | 30 | 75 | 2.0x1.0x1.5 |
VMF-8 | 22 | 40 | 125 | 3.0x1.0x2.0 |
VMF-10 | 40 | 50 | 200 | 4.5x2.0x4.0 |
VMF-12 | 65 | 60 | 265 | 4.5x2.0x4.0 |
VMF-15 | 100 | 75 | 380 | 5.0x2.0x4.0 |
VMF-18 | 160 | 120 | 530 | 5.0x2.0x5.0 |
VMF-20 | 210 | 150 | 650 | 5.0x2.0x5.0 |
VMF-24 | 400 | 250 | 1050 | 5.0x3.5x6.0 |
VMF-30 | 720 | 450 | 1725 | 6.0x3.0x7.5 |
- Production capacity, fineness and HP are normal only and vary from case to
case depending upon several factors. - Specifications and design are subject to change without notice
- Different design can be offered for different applications
- Average feed size of materials is 200 mesh with operating pressure in
between 7-8kg /cm2, but result widely depend on material characteristics